Assessing the Quality of Feeds
The objective of quality control of feedstuffs is to ensure that a consumer should obtain feeds or that cattle are fed feeds that are unadulterated, true to their nature and produce desired results. Quality control is, therefore, defined as the maintenance of quality at levels and tolerances acceptable to the buyer while minimising the cost of processing.
Superior livestock begins with quality feedstuffs and a sound nutritional system. All producers should establish quality standards and acceptance/rejection criteria for all feed ingredients to account for and control variation in feed composition and quality. Rations should be fresh, palatable and uniformly nutritious. Spoiled and/or mouldy feed should be discarded, this helps minimise ration contamination and potential for reduced Dry Matter (DM) intake.
The efficiency of feed utilisation in livestock development is dependent upon the quality of feeds. The quality of feeds is based on the quality of its constituents for example the raw materials such as cereals, cereals by-products, oilseed meals, marine feeds, and agro-industrial by-products, used to formulate the ratio.
Quality has been defined as “any of the features that make something that it is” and “the degree of excellence which a thing possesses.” A quality feed would supply all nutrients in adequate quantity and high digestibility.
Quality Commitment and Points to Evaluate
To organise an in-plant quality control program, an overview of the local operation is the primary consideration, and the development of a quality control manual is a logical first step as a useful guide to action, an employee training tool and a reference for all company personnel. A typical quality control manual will usually have the following:
- An index or outline of content.
- A statement of the company’s quality control philosophy.
- In-plant quality control supervisory and operator duties and responsibilities.
- Sampling practices and procedures for ingredients.
- A suggested ingredient assay schedule.
- Laboratory report including interpretation as to their use.
- Regulation and compliance (Good Manufacturing Practices).
- Production record keeping and procedures.
- Compliant procedures.
- Product recall procedures.
- Rework material guidelines.
- Housekeeping (sanitation) requirements.
- Ingredient purchasing specification.
- Warehousing and pest control practices.
- Shelf-life and finished product turnover standards.
- Guidelines for medicated feed manufacturing and handling.
- Plant formula guidelines/standard operating practices for the handling of new and old formulas.
- Employee training in quality.
- In-process sampling, testing method and test equipment for particle size reduction, batching and mixing, pellet quality, etcetera.
- Maintenance practices and responsibilities.
- Assignment of one person for total coordination of the program. The person should be given clear authority to articulate conditions and problems to management and should not be restricted in that by purchasing, production, sales or any other person or function.
- All plant personnel, including delivery personnel, should be involved in the program and trained to perform their individual quality control duties.
- All quality control stations receiving the various processing locations such as grinding, mixing, pelting, and others, and bulk loadout, should be provided with the necessary test equipment, forms of recording test results, sample bags and other supplies.
- Periodic routine compliance inspections should be conducted by appropriate management personnel using a checklist to ascertain that the company’s quality commitment standard levels are being met, and the results of those inspections should be shared with all levels of management as well as with the plant sand truck fleet employees.
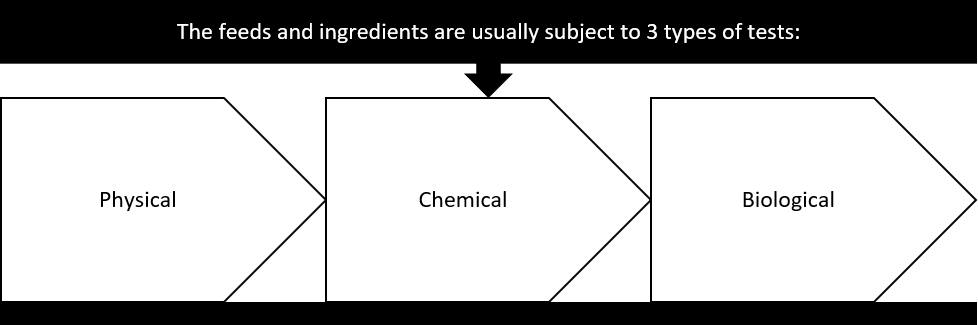
Click on the link below to open the resource.
Sampling Procedure