The requirements of the person performing risk assessments are based on the Construction Regulation 2014 legal requirements.
The designated person performing the risk assessments must be a competent person responsible for the preparation of a fall protection plan.
The fall protection plan developer must have the following training:
Unit standard 229998: Refers to the following assessment criteria to explain and perform fall arrest techniques when working at height and suitable for performing work at height under supervision:
The following indicates the assessment according to worksite procedures:
- Compatibility of equipment of includes but is not limited to the size of anchor, sharp items, prevent damage, point loading, and size of hook.
- Connectors include but are not limited to maillots (stretching fabric), locking carabiner, double action snap hook, pylon hook, and double action scaffold hook.
- Energy absorber includes fall arrest harness and works positioning system, Energy absorbing lanyards include.
- Fall arrest equipment includes a full body harness, helmet, work positioning system, lanyard and energy absorber, shock-absorbing lanyard, and retractable lifeline.
- Fall arrest system includes energy absorbing lanyard including 2 singles, v-type, double legged lanyard or double lanyard.
- Hardware includes connectors, a locking carabiner, and double action hooks. Inspection criteria for hardware include checking hardware for damage, deformation and functioning.
- Lanyards include single-legged lanyards and work positioning lanyards.
- Legislation governing the safety of work at height includes awareness of the existence of legislation and regulations.
- Limitations of an energy-absorbing lanyard include distances (2m).
- Medical surveillance/physical requirements.
- Employees utilizing personal fall arrest systems are expected to be physically fit with no physical conditions that could be aggravated by, or cause the employee harm if he or she was involved in a fall and was to rely on the fall equipment for life safety.
- These include but are not limited to heart disease, high blood pressure, epilepsy, fits and blackouts, fear of heights, giddiness or difficulty with balance, impaired limb function, alcohol or drug dependence, psychiatric illness, and diabetes.
- PPE include but is not limited to helmets with a chinstrap, gloves, goggles, safety footwear, close-fitting overalls or items specified for the task. Inspection criteria for helmets include damage and intact chinstrap.
- Risks while awaiting rescues can include suspension trauma, position, physical injury, injury from hot surfaces, electricity, fumes, and water. Feet to be kept moving to prevent the reduced flow of blood to the brain that can lead to unconsciousness or death.
- Slings include but are not limited to certified tape slings, wire slings and rope slings.
- The software includes a harness, work positioning harness, and absorbing lanyard. Inspection criteria for software include checking the stitching, webbing, identification or labels, buckles, D-rings and connectors.
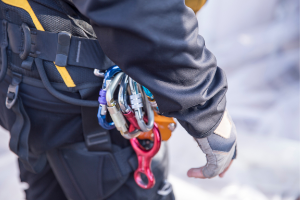
Unit standard 229995: refers to assessment criteria suitable for performing work at height under supervision.
- Install, use and perform basic rescues from fall arrest systems and implement the fall protection plan.
- The fall protection plan developer must ensure that the fall protection plan is implemented, amended where and when necessary maintained and the Project Manager must have the latest copy of the fall protection plan at all times.
- The Project Manager must ensure compliance with the fall protection plan and take steps to ensure continued adherence to the fall protection plan.
- The person doing the Risk Assessment should have knowledge of the type of work, the type of exposure, the employees or people that are exposed, relevant legislation and the type of control measures to be put in place.
- You must consult your staff or their representatives in the risk assessment process. They will have useful information about how work is done which will help you understand the actual risks.
- You may find that there are a number of issues which need action, so you need to decide on your priorities for that action. In thinking through your priorities, think about the biggest or most serious risks first.
Having identified the priorities, you need to decide on the controls which you will put into place. In doing so, think about the following:
- Long-term solutions to those risks with the worst potential consequences.
- Long-term solutions to those risks are most likely to cause accidents or ill health whether there are improvements that can be implemented quickly, even as a temporary solution until more reliable controls are in place.
- Remember, the greater the risk the more robust and reliable the control measures will need to be.
- Recognize and control hazards and exposures in the workplace.
- Create awareness among employees and also use it as a training tool. Set risk management standards based on acceptable self-practice and legal requirements.
- Reduce incidents in the workplace and save costs by being proactive instead of reactive.
- To effectively identify hazards and assess risks in the workplace, you’ll need the assistance of all your employees.
Remember the process doesn’t stop with the identification and assessment of hazards and risks. Once the first part of the process has been completed, risk management actions need to be taken. Through awareness and training, you’ll ensure compliance with risk management requirements and a high level of system effectiveness.