Safe work procedures (SWP) are required when the risk of injury to workers performing a job task cannot be eliminated by effective work design, work process or equipment. Employers must ensure SWPs are based on information gathered by a risk assessment. They must also be developed in consultation with your workplace safety and health committee or representative and be approved by management. Workers must be trained in the safe work procedures so they understand the steps and equipment they must use to work safely. Supervisors must ensure that safe work procedure is followed. Safe work procedures should be readily available to workers for reference.
Safe work procedures do not have to follow a particular format, however, your safe work procedures should include:
- Name or description of the work task.
- Date the SWP was created and the date it was last reviewed or revised.
- Hazards that may cause harm to a worker.
- Common signs and symptoms of a musculoskeletal injury if the hazards of the job task could lead to this type of injury.
- Equipment/devices, personal protective equipment (PPE), or other safety considerations are necessary to perform the task safely.
- Required training/relevant documentation needed to perform the task safely.
- Steps to perform the task safely including safe body positions/movements as appropriate.
- An indication that workers are to be trained on the SWP and employers must ensure workers follow them.
Remember to review your safe work procedures regularly to ensure they are accurate and effective. If a task or equipment changes, the safe work procedure(s) that relate to this change must also be updated.
OHS Act requires that fall protection be provided at elevations of 1.2m in general industry workplaces and 1.8m in the construction industry.
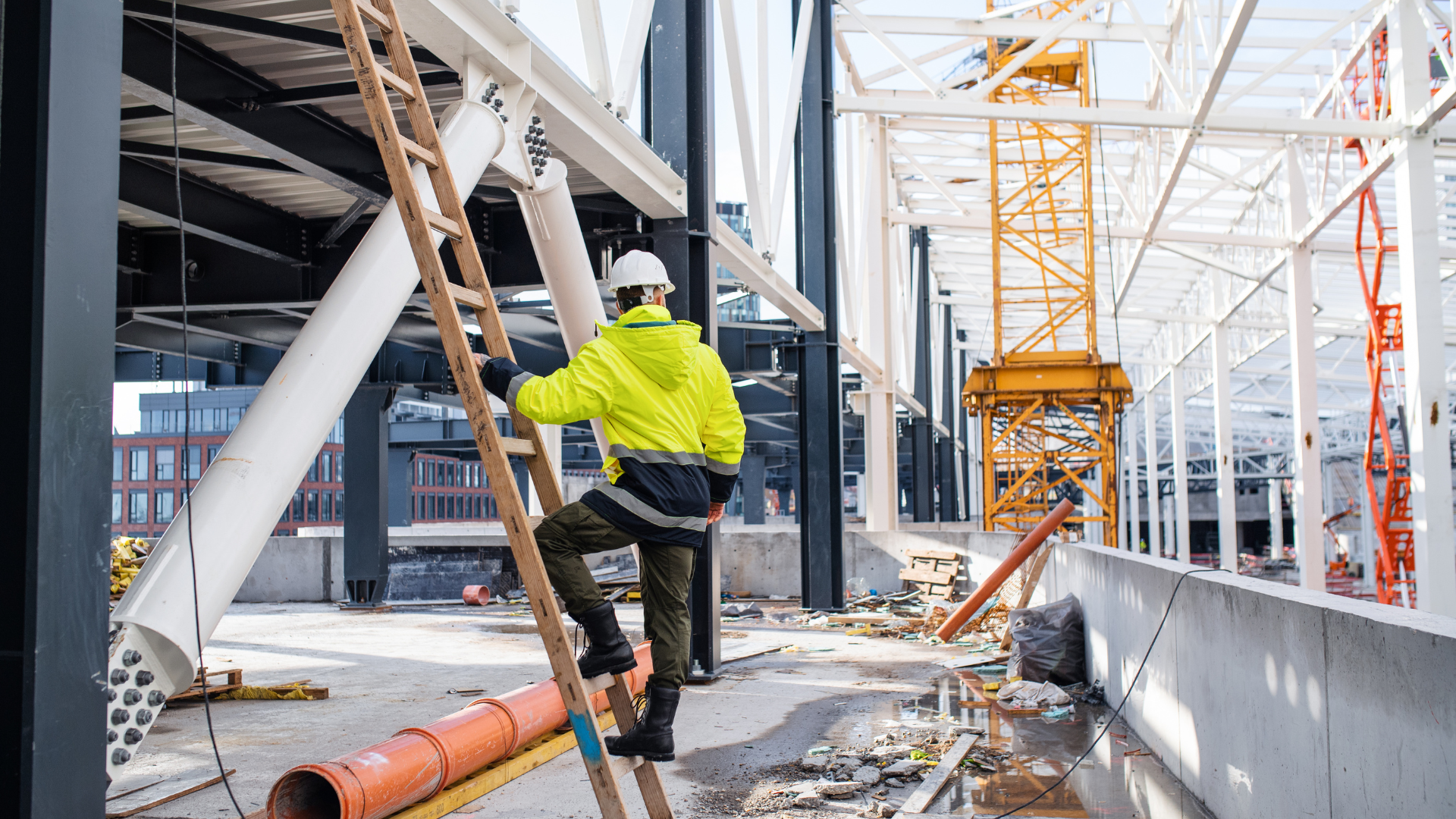
Example 1
Objective:
The objectives of this procedure are to provide rules and procedures to protect employees from the hazards of working at heights and to establish mandatory requirements for practices to protect personnel from hazards associated with Working at Heights.
Scope:
This SWP applies to all operating and project sites of the ABC group of companies involved in Work at Height Jobs.
Expected Results:
- Manage Work at Height jobs being done under Permit-To-Work safely.
- Control of incidents related to Work at Height jobs.
- Compliance with regulatory requirements to make the workplace safe.
Safe Work Procedure:
- Proper scaffolds/temporary work platforms shall be provided for working at height at elevations of 1.8m or more where no permanent work platform is available to work safely. The elevated work platforms shall have guardrails and be provided with ladders for access/egress.
- Where it is not feasible to erect scaffolds, suitable hydraulically elevated work platforms or portable platforms with wheel locks/chokes and guardrails shall be used.
- Ladders shall not be used as work platforms.
- Employees or contractors working on unguarded surfaces, steep slopes and similar locations; temporary platform, during scaffold construction; or when otherwise exposed to the possibility of falls hazardous to life or limb, shall be secured by full body harness with double lanyard.
- Full body harness with double lanyard shall be worn when work requires persons closer than 1.8 meters from the roof edge without parapets or floor opening. Note: Uncontrolled once printed
- Full body harness with double lanyard shall be used by persons where work requires persons to move or walk from one place to another for changing work locations at height and where it is not feasible to provide guarded platforms and scaffolds (e.g. pipe racks) so as to ensure one lifeline is always tied with fixed support.
- Persons shall always keep one lanyard anchored/tied with the fixed support while walking/moving on unguarded surfaces/edges or structures.
- Where ever appropriate fixed support is not available to anchor the lanyard of full body harness, lifelines certified by a qualified inspector shall be used to anchor the lanyard.
- The intended load shall not exceed the maximum working load of portable work platforms.
- Full body harness, lanyard and snap hook, which conform to SABS standard, (SANS 10085-1993) shall be used. Safety belts are prohibited.
- A lanyard shall be attached to the D-ring on the back of the full body harness between the shoulder straps.
- Snap hooks shall be of double locking type.
- Fall arresting devices may be used depending on the requirement of the situation, i.e. painting, wall painting, working on the towers, etc.
- Anchor points for fall arresting systems must be capable of withstanding (as per SANS 10085-1993) l per person attached.
- Personal Fall Arrest System components shall be visually inspected before each use.
- Proper area barricading to prevent people from walking across below the working area shall be done before commencing any work at height. If such barricading is not possible, a safety net shall be provided and “Work in Progress” boards shall be displayed.
- A process shall be in place to ensure employees are medically fit to perform their duties and that their health is not adversely affected by occupational hazards.
- No working at height shall be carried out without supervision.
- Job Safety Analysis (JSA) shall be conducted for Working at Height which includes access & egress from one anchorage point to another anchorage point.
- Permit-To-Work Procedure shall be followed for all Work at Height.
- Working at Height after daylight hours shall be authorized by the Project Manager with appropriate control in place.
- When performing man lift operations, all personnel in the personnel basket (platform) shall wear a full body double harness with the lanyard attached to the man lift or permanent structure.
- Scaffolding shall be erected as per the scaffolding procedure.
- In case of hazard of honeybees, help from pest control, water spray, steam jet and PVC apron with hood shall be used.
- Installation of a guardrail system around the work area is required for fall protection.
- Guardrail systems shall meet the following minimum requirements:
-
- The top rail (handrail) shall be 1200mm from the working surface.
- Top rails must be capable of withstanding an expected force which may arise while working.
- Mid-rails shall be located midway 600mm between the top rail and the working surface.
- The mid rail must be capable of withstanding a force of 70kg.
- Toe boards should be provided to prevent persons from falling off the working surface.
- Screens or panelling from the toe board to the mid or top rail should be required when equipment or material is piled higher than the toe board and is capable of being ejected from the working surface to the level below.
- Where gates or openings are required in the guardrail system to facilitate material movement, personal fall arrest or restraint systems shall be used.
- All platforms/walkways above 1.8m from the floor shall be provided with a guardrail system.
- Every floor opening into which any person can fall shall be guarded by a standard guardrail system or by a grating duly fixed in position.
- Any floor opening, for temporary maintenance work, shall be fixed with a proper size cover having sufficient strength.
- Fall arrest systems mitigate the consequences of a fall. The system consists of a proven anchor point, connectors, full body harness, and lanyard and deceleration device. The entire system shall be capable of withstanding impact forces involved in stopping or arresting the fall. Consideration must be given to what is below the area of work and what the person may strike during the fall.
- Fall Protection system is a full body harness with a double line lanyard of 1.8m length out of which, one has to go to the fixed anchorage and another one for movement. Shock absorbers are preferred to ascertain the adequacy of the harness in case of a sudden fall.
- Safety nets shall be provided for protecting from human falls and material falls.
- Hand tools used while working at height should be securely tied to avoid free fall in case of accidental slippage. Personal Fall Arrest System components shall be visually inspected before each use.
- Lifelines shall be installed or modified only by qualified installers.
- When more than one person will be utilizing a lifeline simultaneously, the load allowance of the lifeline shall be increased so as to provide the same level of support as it did while one person was using it. This use has to be approved by a qualified person.
- Provision shall be made for routine inspection and maintenance of all ladders. Broken or damaged ladders shall be promptly repaired or removed and destroyed.
- Securing ladders: All ladders shall be placed on firm ground, secured at the top and intermediate positions to maintain them rigidly in place and to support the loads imposed upon them.
- Restrictions: Ladders will not be used as work platforms or scaffolding or as structured members of scaffolds or walkways.

Review: Review of this procedure shall be done as and when but not later than once every three (3) years. Typical factors like changes in legislation, review of incident reports, inspection and audit findings, feedback from users, and recommendations in Incident investigation reports may be input for the review and revision of the procedure.
Construction workers should only work at heights when it is absolutely unavoidable. When the green light is given to work at height, the effective implementation of a standard procedure can drastically reduce the associated risks and hazards.
Below is an example of a standard procedure when working at heights:
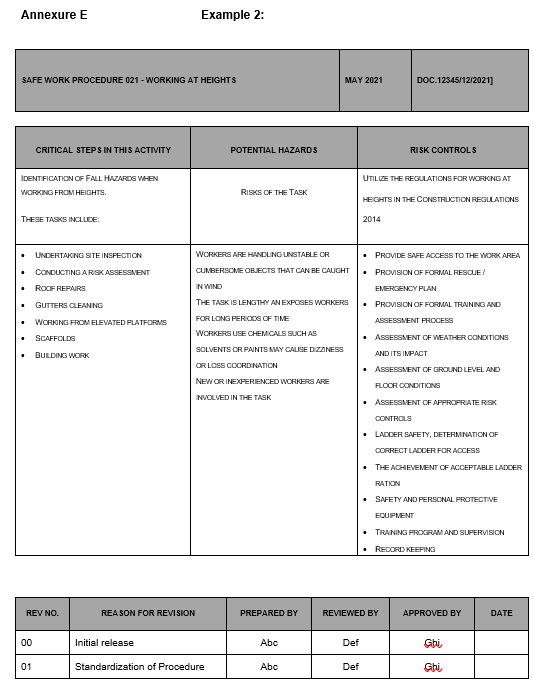
Click here to view or download Annexure E.
Monitoring
Process Monitoring:
This is referred to as ‘activity monitoring.’ Process monitoring is implemented during the initial stages of a project as its sole purpose is to track the use of inputs and resources, along with examining how activities and outputs are delivered. It is often conducted in conjunction with compliance monitoring and feeds into the evaluation of impact.
Compliance Monitoring:
The purpose of compliance monitoring is to ensure compliance with contract requirements, local governmental regulations and laws, and most importantly compliance with the expected results of the project. The need for compliance monitoring could arise at any stage of the project life cycle.
Related/Supporting Documents:
- Appointment of a Fall Arrest System inspector.
- Inspection checklist for FAS (Fall Arrest Systems).
- Personal Protective Equipment for Work at Heights specification.
- Risk assessment template.
- Fall Protection Plan compiler.
- Inspector of FAS – CR 10 (2)(d).
- PPE for Work at Heights specification.
Context Monitoring:
Context monitoring is also called ‘situation monitoring.’ It tracks the overall setting in which the project operates. Context monitoring helps us identify and measure risks, assumptions, or any unexpected situations that may arise within the institutional, political, financial, and policy context at any point during the project cycle. These assumptions and risks are external factors and are not within the control of the project, however, context monitoring helps us identify these on time to influence the success or failure of a project.
Process Evaluation:
It is conducted as soon as the project implementation stage begins. It assesses whether the project activities have been executed as intended and resulted in certain outputs. Process evaluation is useful in identifying the shortcomings of a project while the project is still ongoing to make the necessary improvements. This also helps to assess the long-term sustainability of the project.
Outcome Evaluation:
This type of evaluation is conducted once the project activities have been implemented. It measures the immediate effects or outcomes of the activities and helps to make improvements to increase the effectiveness of the project's health, safety and environment.