
To ensure a safe working environment and to enable one to adequately deal with accidents such as fires and spillage, proper storage of CPPs is essential. The basic principles are as follows:
- Store CPPs in a secure, well-ventilated, cool and dry building that does not allow access to children, animals or unauthorised persons.
- There must be easy access to washing facilities with running water, soap and towels. It is important that an eye-flushing bottle is available in the event that the eyes are contaminated.
- The storage facility should have a smooth, damp-resisting cement floor.
- The storage facility should have at least two 9 kg dry-powder fire extinguishers on hand. These must be located outside the storeroom.
- No food products, animal feed or seeds may be taken into the facility.
- Do not allow any eating, drinking or smoking in the storage facility.
- Separate pesticides, fungicides, herbicides and growth regulators from each other within the storage area. Ensure that each storage area is well demarcated so that there can be no accidental mixing of products. It is recommended that herbicides are stored completely separately.
- Keep powders and granular products stored separately to avoid contamination in the event of spillage. Always store powders and granules on the upper shelves and liquids on the lower shelves.
- Group stored CPPs according to their hazard potential, e.g. store red-band (group 1a and 1b) CPPs in the same part of the store.
- Products should be used on a first-in-first-out basis. This should ensure that CPPs are used before reaching their expiry date.
- Bags and containers that are not placed on shelves should be stacked on pallets to prevent a build-up of moisture.
- All containers and bags must be adequately marked. In the event that a label is destroyed or lost, the container must be marked with a marking pen, clearly stating the container’s contents. The label should always be visible.
- An accurate stock movement recording system, indicating the quantities of each CPP purchased, issued and subsequently returned, must be in place. From the recording system, one should be able to determine the exact type and quantity of CPPs on hand at any given time.
- The containers of CPPs that have been opened and partly used should be resealed and returned to the store.
Disposal Of Empty Containers
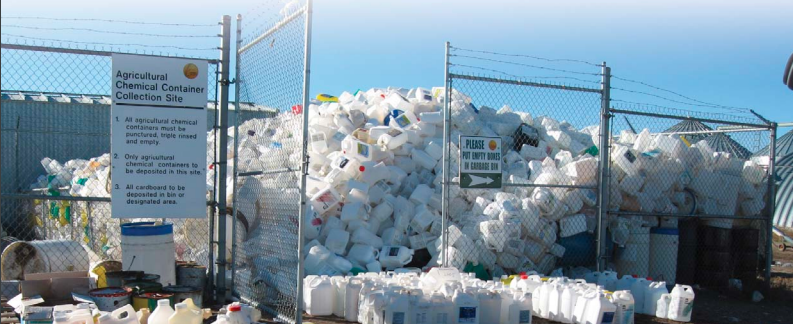
Empty CPP containers must under no circumstances be re-used for any purpose whatsoever. Even if the container has been washed thoroughly the risk of contamination remains high. Empty containers must be disposed of in the manner described below.
Empty containers must be rinsed by filling it to about a quarter with clean water, closing and shaking them well. Pour the rinse water into the spray tank. Repeat this process at least three times. Puncture the container after rinsing to ensure that it cannot be re-used.
Once containers have been punctured, they should be diminished (flattened) in bulk and buried at a disposal site in a pit. The disposal site must be:
- At least 50m from the nearest water source (dam, river and borehole).
- On relatively high ground or where the groundwater is at least 2m deep.
- Not in sandy soils that leach easily.
- Fenced in and a signpost.
Waste bags, paper and mildly contaminated items must be burned, while severely contaminated items and redundant CPPs must be disposed of using a high-temperature incinerator, which can also be used for empty containers. A professional waste disposal company may be contacted in this regard.
General Sanitation
Ensure that a wash trough or large basin is available in or close to the CPP storage facility. This will allow the washing of contaminated clothing on-site and prevent staff from wearing the clothing home where it may or may not be washed.
Equipment, such as scoops, buckets, measuring cups, etc. must be washed at the end of a working day. All protective clothing and equipment must be kept in good condition and cleaned regularly.
Have a spade, broom and a supply of dry sand on hand which can be used in case of CPP spillages. Sawdust must never be used for this purpose as it presents a fire hazard, and when mixed with certain CPPs, can result in an explosion.
Important Notes
- PPP used for foliar applications must be mixed correctly and accurately immediately before application.
- The person responsible for mixing the chemicals must take note of the safety requirements when handling the chemicals by checking the colour codes, symbols and pictograms that are used on the product labels.
- Colour codes are used to indicate the hazard classification of the chemical.
- Internationally recognised symbols are used to indicate the toxicity of chemicals that are extremely, highly and moderately hazardous.
- Pictograms are used to indicate other information about the product, including the required protective gear and clothing.
- Apart from the chemicals, protective clothing, measuring equipment and mixing equipment are required during the mixing process.
- The amount of chemicals that are required is calculated from the crop protection program. The same volume of water as the volume of spraying material that is required is used as a basis.
- Buffers are used to adjust the pH of water.
- Spraying oils often form part of spraying materials because they assist in controlling pests and diseases.
- The mixing procedure involves measuring the correct quantities of chemicals, mixing these in a bucket, adding the mixed chemicals to half the volume of water in the spray tank and adding the remainder of the water while stirring the mixture.
- Plant protection products must be stored in a safe, secure room that complies with GAP requirements.
- Empty chemical containers must not be re-used for any purpose. They must be rinsed, punctured and disposed of, either by being buried or by being incinerated.
- All protective clothing and equipment must be washed after use.